The Pivotal Role of Injection Mold Plastic in Modern Manufacturing
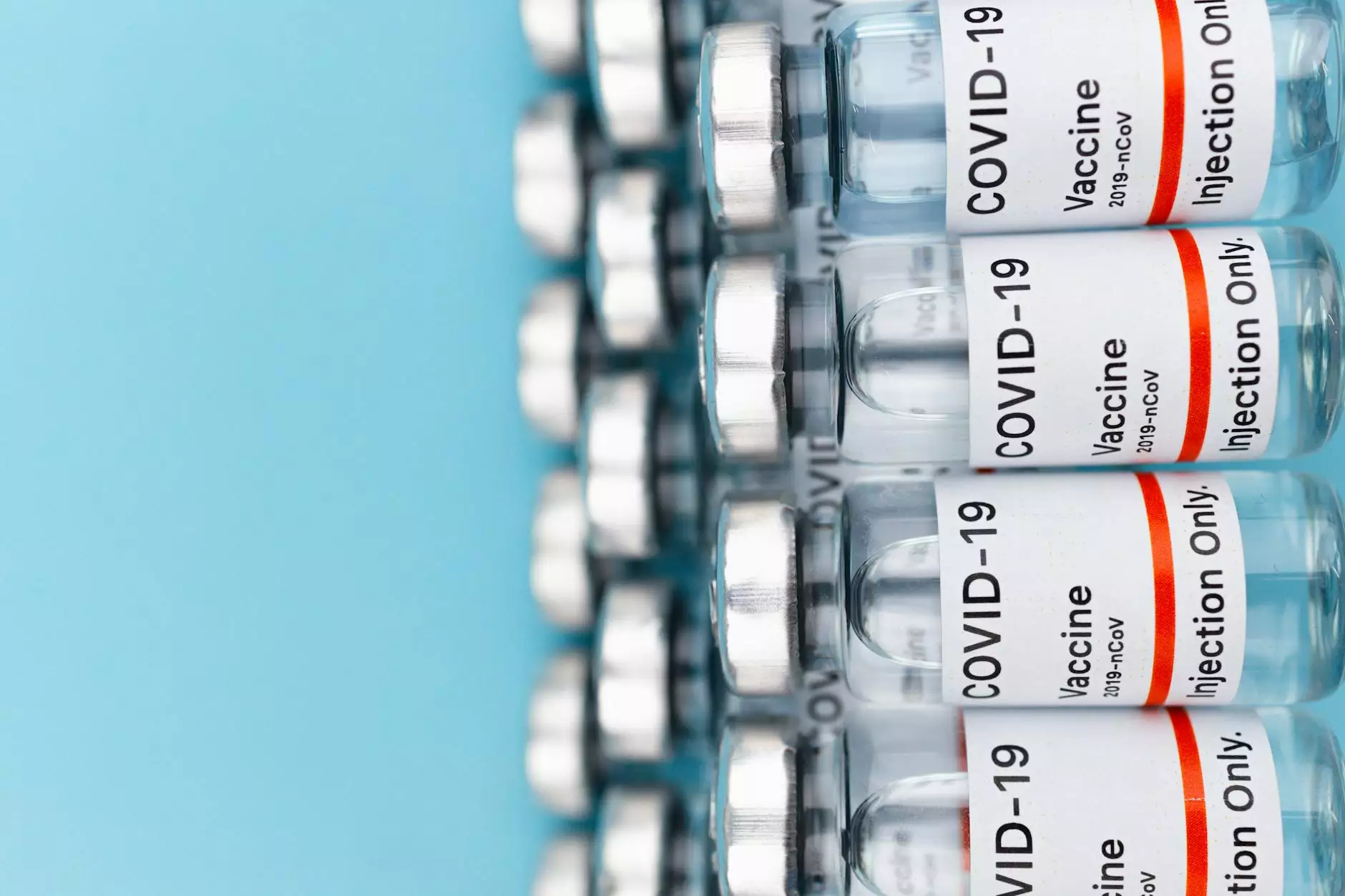
In today’s fast-paced manufacturing landscape, injection mold plastic stands out as a cornerstone of innovation and efficiency. This technique allows for the precise shaping of plastic materials into intricate forms that meet the varying demands of industries ranging from automotive to consumer goods. Understanding its intricacies can significantly enhance a company's production capabilities and product quality.
The Basics of Injection Molding
Injection molding is a manufacturing process used to create parts by injecting material into a mold. The process is highly efficient and can produce a wide variety of shapes, sizes, and complexities. Here’s a breakdown of the basic steps involved in injection molding:
- Material Selection: The first step involves selecting the right type of plastic. Common materials include thermoplastics and thermosetting plastics, each offering unique properties.
- Mold Design: A mold is designed based on the desired shape of the final product. This can be a complex process depending on the intricacy of the design.
- Injection Process: The plastic granules are heated until they melt and are then injected into the mold under high pressure.
- Cooling and Solidifying: Once the mold is filled, the plastic is allowed to cool and solidify, taking the shape of the mold.
- Mold Removal and Finishing: The finished part is removed from the mold, and any necessary finishing touches are applied.
Advantages of Injection Mold Plastic
Utilizing injection mold plastic brings numerous advantages that can greatly enhance manufacturing operations. Some key benefits include:
- High Efficiency: Injection molding allows for the production of large quantities in a short time, making it perfect for high-volume manufacturing.
- Precision and Consistency: This method ensures tight tolerances and a high level of replication, leading to consistent quality across all produced parts.
- Material Versatility: A wide range of materials can be used, allowing manufacturers to choose the best plastic for their specific application.
- Lower Labor Costs: Once set up, the automation of injection molding requires less manual labor, reducing overall production costs.
- Reduced Waste: The process is designed to use materials efficiently, leading to minimal waste compared to other manufacturing methods.
Applications of Injection Mold Plastic in Various Industries
The versatility of injection mold plastic allows it to be used in multiple industries. Below are some significant sectors where this process shines:
1. Automotive Industry
In the automotive sector, components such as dashboards, panel covers, and various interior parts are manufactured using injection molding. The ability to create complex geometries enables designers to innovate while maintaining structural integrity.
2. Consumer Products
Everyday products like containers, toys, and appliances often rely on injection-molded parts. This method not only reduces production costs but also enhances the product's design appeal.
3. Medical Devices
In the medical field, precision and hygiene are paramount. Injection molding allows for the mass production of sterile and high-precision components such as syringes and implants, ensuring that they meet strict regulatory standards.
4. Electronics
Many electronic devices are housed in injection-molded enclosures. This manufacturing method accommodates complex designs while ensuring that products are both durable and lightweight.
Understanding the Injection Molding Process
Delving deeper into the injection mold plastic process reveals several intricacies that affect efficiency and quality. Here’s a closer look at the stages involved:
1. Material Preparation
The journey begins with the preparation of the plastic pellets. These pellets are dried and heated to the right temperature for optimal melting capabilities. The choice of material can significantly influence the final product's properties, including strength, flexibility, and resistance to chemicals.
2. Injection Cycle
The injection cycle consists of several phases:
- Clamping: The mold is closed securely to prevent leakage during injection.
- Injection: The molten plastic is injected into the mold at high speed and pressure.
- Cooling: After the mold is filled, the plastic cools down, solidifying into the desired shape.
- Opening: The mold opens, and the finished part is ejected.
3. Troubleshooting Common Issues
Despite its benefits, challenges can arise in the injection molding process. Common issues include:
- Pocket Formation: This occurs if the mold isn't filled properly, leading to empty spaces within the part. Ensuring correct injection speed and pressure can help mitigate this.
- Surface Defects: Imperfections such as sink marks or short shots can arise from improper cooling or material choice. Adjusting cooling times and mold design can alleviate these problems.
Future Trends in Injection Molding
As technology evolves, the field of injection mold plastic is set to experience significant advancements. Key trends to watch include:
1. Sustainable Practices
With growing concerns about environmental impact, manufacturers are increasingly looking for sustainable materials and practices. Biodegradable plastics and energy-efficient machines are gaining traction.
2. Advanced Automation
The incorporation of AI and robotics into the injection molding process is on the rise. These technologies promise improved precision, predictive maintenance, and enhanced efficiency.
3. Industry 4.0 Integration
Integrating IoT (Internet of Things) into injection molding processes allows for real-time monitoring and adjustments, enhancing operational efficiency and product quality.
Conclusion: The Impact of Injection Mold Plastic on the Future of Manufacturing
In summary, the realm of injection mold plastic is vast and full of opportunities. Its ability to manufacture high-quality parts efficiently makes it an essential technique in various industries. As trends toward sustainability and automation continue to evolve, the potential of injection molding will only grow. Companies like deepmould.net, specializing in metal fabrication and plastic injection molding, are at the forefront of this exciting journey, ready to lead the way into a future defined by innovation and quality.
This detailed understanding of injection molding processes and its applications will not only help businesses optimize their production but also position them strategically in a highly competitive market. As you consider your manufacturing needs, remember, the potential of injection mold plastic is limited only by your imagination and willingness to innovate.