The Ultimate Guide to Vertical Cartoners
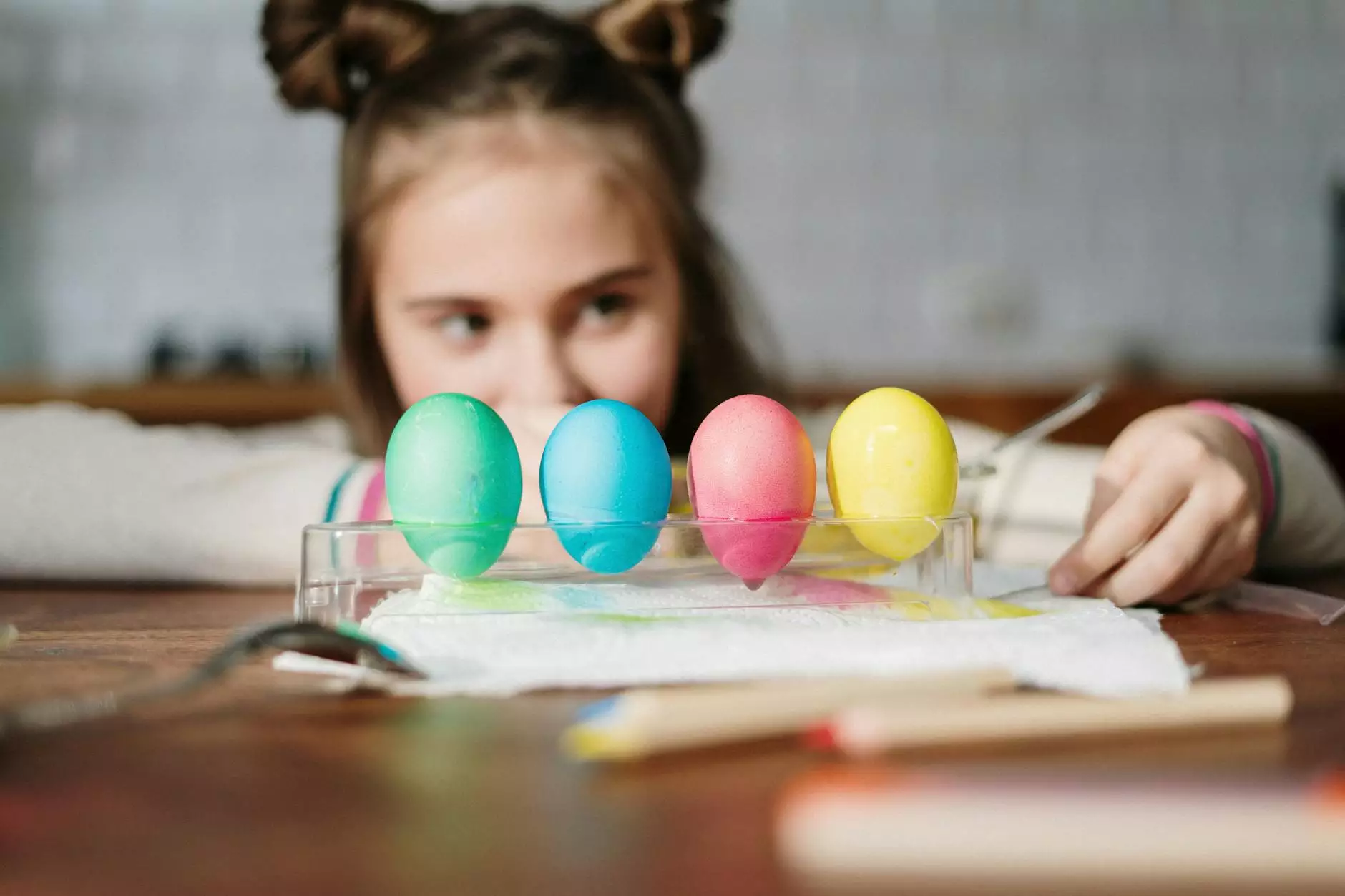
In today’s competitive market, efficiency and quality in packaging are crucial for maintaining a successful business. One of the most effective solutions to achieve this is through the use of vertical cartoners. These machines offer a wide array of benefits that can significantly enhance the packaging processes of various products. In this comprehensive guide, we will delve deep into the role of vertical cartoners in the packaging equipment industry, focusing on their advantages, applications, and what makes them an invaluable asset for manufacturers. Let’s explore how investing in vertical cartoners can transform your business operations.
What is a Vertical Cartoner?
A vertical cartoner is a specialized piece of machinery designed to form, fill, and seal cartons for a variety of products. Unlike horizontal cartoners, which operate in a flat orientation, vertical cartoners work in an upright position. This design allows for efficient space utilization and is particularly advantageous for packaging products such as bags, pouches, and even small boxes.
Why Choose Vertical Cartoners?
The decision to implement vertical cartoners in your packaging line comes with numerous benefits:
1. Enhanced Efficiency
Vertical cartoners are designed for high-speed operations, allowing manufacturers to package large volumes of products in a shorter amount of time. This increases overall throughput, enabling businesses to meet growing market demands without compromising quality.
2. Space-Saving Design
Due to their compact nature, vertical cartoners occupy less floor space compared to horizontal models. This is particularly beneficial for manufacturers operating in facilities with limited space, allowing them to optimize their layout and resource allocation.
3. Versatility
Vertical cartoners can handle a wide range of products and packaging materials. Whether you are packaging snacks, pharmaceuticals, or consumer goods, these machines can be customized to suit your specific needs. This versatility makes them a valuable investment for diverse manufacturing sectors.
4. Improved Quality Control
With integrated sensors and automated controls, vertical cartoners ensure precise filling and sealing of cartons, significantly reducing the chance of errors. This results in consistent product quality, which is crucial for maintaining customer satisfaction and brand reputation.
Applications of Vertical Cartoners
The versatility of vertical cartoners enables their application across various industries:
- Food and Beverage: Ideal for packaging snacks, frozen goods, and drinks.
- Pharmaceuticals: Used for packaging medicines and supplements safely.
- Cosmetics: Suitable for packaging personal care products efficiently.
- Household Products: Perfect for packaging cleaning supplies and detergents.
Comparing Vertical and Horizontal Cartoners
While both vertical and horizontal cartoners have their unique advantages, understanding their differences is essential for making an informed choice. Here’s a brief comparison:
Design and Space Usage
Vertical cartoners typically require less floor space, making them ideal for facilities with spatial constraints. Their upright design allows for more efficient use of vertical space, whereas horizontal cartoners may need larger areas to accommodate their layout.
Processing Speed
Vertical cartoners often outperform horizontal models in terms of speed, thanks to their streamlined processing capabilities. This efficiency is readily observable in high-demand environments where every second counts.
Product Compatibility
Vertical cartoners excel in handling lightweight, flexible packages, while horizontal cartoners are better suited for heavier, sturdier items. Depending on your product specifications, one may prove more advantageous than the other.
The Mechanism of Vertical Cartoners
Understanding the workings of vertical cartoners can shed light on their efficiency:
1. Carton Erecting
The process begins with the vertical cartoner erecting a flat carton into a usable form. This is often achieved automatically, allowing for rapid transitions between packaging cycles.
2. Filling and Sealing
Once the carton is formed, it is filled with the product and sealed. Various filling methods can be applied, depending on the product type, with options for volumetric, weight, or timed filling systems.
3. Final Inspection
The last stage involves a quality control check where automated sensors verify that the carton is filled correctly and sealed securely.
Choosing the Right Vertical Cartoner
Selecting the appropriate vertical cartoner involves considering various factors:
1. Product Specifications
Evaluate the type of products you will be packaging. Factors such as size, weight, and material can significantly influence the type of vertical cartoner you need.
2. Production Capacity
Determine your production needs. Higher production demands may require more advanced cartoning machinery with greater speed and functionality.
3. Customization Options
Look for machines that offer customizable features, allowing you to adapt the equipment as your business needs evolve.
4. After-Sales Support
Invest in a manufacturer that provides excellent after-sales support, including maintenance and troubleshooting assistance. This can save you time and costs in the long run.
Maintaining Your Vertical Cartoner
To ensure longevity and consistent performance of your vertical cartoner, regular maintenance is essential:
- Regular Cleaning: Regularly clean the machine to prevent product buildup and contamination.
- Scheduled Maintenance: Follow a maintenance schedule, including inspections and part replacements as needed.
- Training for Operators: Ensure that staff operating the machinery are adequately trained to handle it properly and identify issues early on.
Innovations in Vertical Cartoner Technology
The packaging industry is constantly evolving, and vertical cartoners are no exception. Recent innovations have introduced:
1. Smart Technology Integration
Many modern vertical cartoners now feature smart technology, allowing for real-time monitoring and data collection. This enhances operational efficiency and streamlines maintenance processes.
2. Energy Efficiency
Advancements in engineering have resulted in more energy-efficient machines, reducing operational costs and environmental impact.
3. Robotics Automation
The integration of robotics into vertical cartoners allows for even greater efficiency, particularly in handling and moving products through the packaging process.
Conclusion: Maximizing Your Investment with Vertical Cartoners
In conclusion, adopting vertical cartoners into your packaging systems can significantly enhance operational efficiency, product quality, and overall business productivity. As a leading packaging equipment manufacturer, Shineben offers state-of-the-art vertical cartoners that cater to the diverse needs of modern manufacturers. By choosing the right vertical cartoner, you position your business to not only keep pace with market demands but also stand out in an increasingly competitive landscape. Invest in the future of your manufacturing line and watch your business thrive!
For more information about our vertical cartoners and other packaging solutions, visit shineben.com today!