The Essential Guide to Oil Seal Manufacturing for Diesel Engines
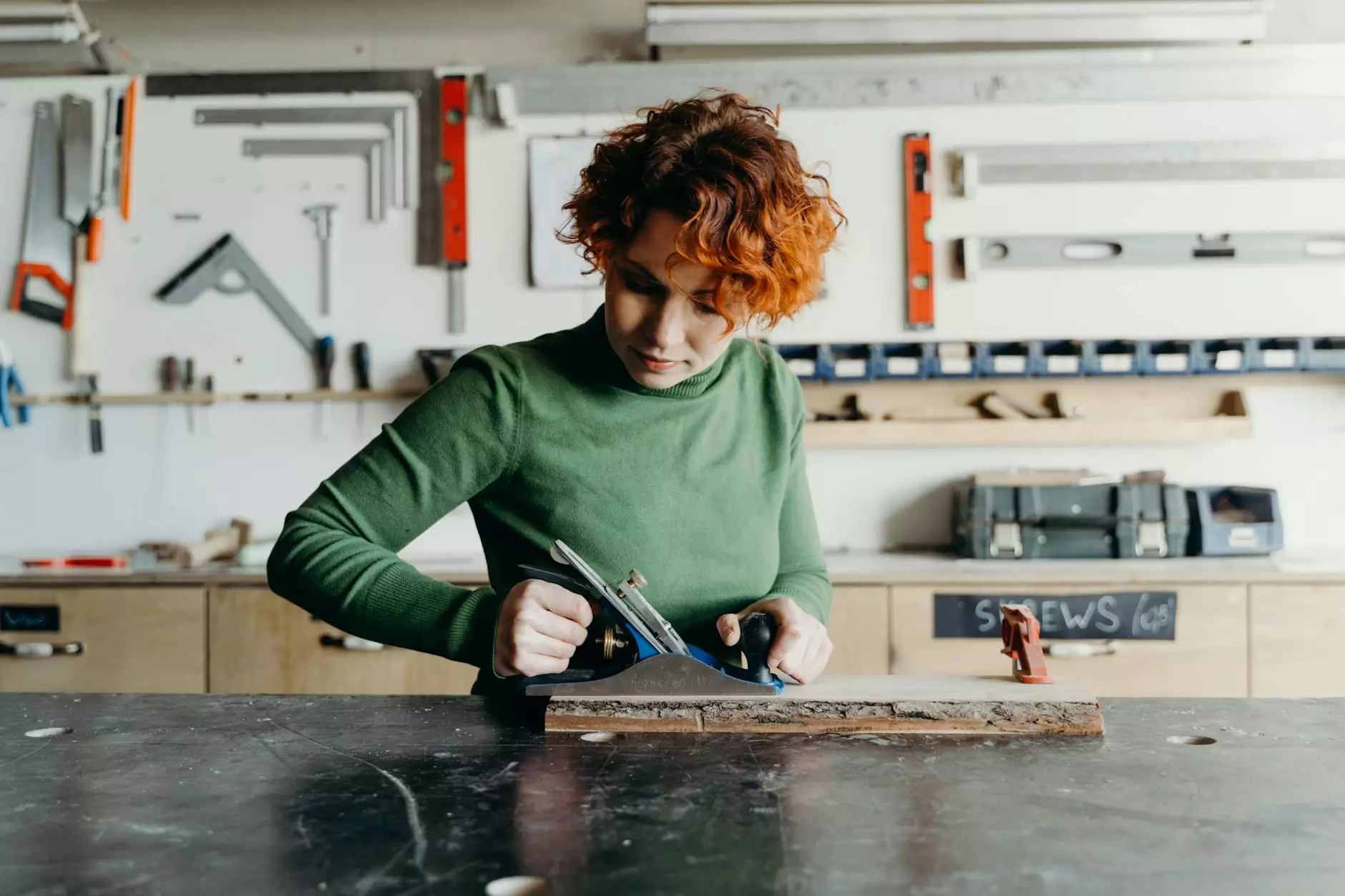
Oil seal manufacturing is a critical component in the realm of diesel engine parts and spare parts suppliers. These seals are pivotal in ensuring that engines function seamlessly by preventing leaks, enhancing performance, and extending the lifespan of machinery. This article delves deep into what oil seals are, the manufacturing process, their applications in various industries, and tips for selecting the best oil seal supplier.
What Are Oil Seals?
Oil seals, also known as shaft seals, are mechanical seals that retain oil within machinery while preventing the intrusion of dust, dirt, and moisture. Typically made from rubber or elastomeric materials, oil seals come in various shapes and sizes tailored to specific applications. They play a harmonious role in maintaining the integrity of the lubricating oil in diesel engines by ensuring that it does not leak out of the system.
The Importance of Oil Seal Manufacturing
The manufacturing of oil seals is essential for several reasons:
- Leak Prevention: Oil seals create a tight seal around moving parts, minimizing the risk of lubricant leakage which can lead to increased wear and tear.
- Dust and Contaminant Protection: They help keep contaminants away from sensitive engine components, ensuring cleanliness and optimal performance.
- Optimal Engine Performance: By maintaining the right oil levels and preventing leaks, oil seals contribute to the overall efficiency and productivity of diesel engines.
- Cost Efficiency: Reliable oil seals minimize maintenance costs by lowering the frequency of repairs and replacements needed for engine components.
Understanding the Oil Seal Manufacturing Process
Oil seal manufacturing is a complex process that requires precision engineering and high-quality materials. Here’s a detailed overview of the key steps involved:
1. Material Selection
The first step in oil seal manufacturing is choosing the right materials. Commonly used materials include:
- Nitrile Rubber: Known for its excellent oil and heat resistance, making it ideal for many automotive applications.
- Fluoroelastomers: Perfect for high-temperature applications and aggressive chemical resistance.
- Polyurethane: Offers superior wear resistance, beneficial in high-load applications.
2. Design Engineering
Once materials are selected, the next step is designing the oil seal. This involves:
- Creating engineering drawings and specifications that outline dimensions and performance criteria.
- Utilizing CAD software to model the seal, ensuring optimal fit and functionality in the intended application.
3. Molding and Production
The actual manufacturing process typically involves two main methods:
- Compression Molding: A method where heated uncured rubber is placed into a mold. The pressure causes the rubber to take the shape of the mold, and once cooled, it hardens to form the oil seal.
- Injection Molding: Involves injecting molten rubber into a mold cavity. This method allows for high precision and is suitable for large-scale production.
4. Quality Control
Post-manufacturing, each batch of oil seals undergoes stringent quality control tests. This includes:
- Dimensional checks to ensure accurate sizes and fits.
- Material testing to confirm resistance to oils, temperature, and physical stresses.
- Performance testing in simulated operating conditions to verify the seals meet industry standards.
Applications of Oil Seals
Oil seals have a broad range of applications across various industries, especially in machinery and vehicles. Some notable uses include:
1. Automotive Industry
In vehicles, oil seals are used in:
- Engine crankshafts
- Transmission systems
- Differentials
They help maintain appropriate lubrication and support engine longevity.
2. Industrial Machinery
Oil seals are vital in numerous types of industrial machinery, including:
- Hydraulic pumps
- Compressors
- Conveyor systems
They protect internal components from contamination and keep lubricants sealed properly.
3. Agricultural Equipment
In the agricultural sector, equipment such as tractors and harvesters rely heavily on oil seals for:
- Ensuring efficient operation during heavy loads
- Extending the lifespan of agricultural machinery
Choosing the Right Oil Seal Supplier
When selecting a supplier for oil seals, there are several factors to consider to ensure you receive high-quality products:
1. Industry Experience
Choose a supplier with a proven track record in oil seal manufacturing. Their experience will often translate to better quality products and customer service.
2. Quality Certifications
Ensure that the supplier adheres to industry standards and has relevant certifications such as:
- ISO 9001
- TS16949 (Automotive specific)
Such certifications reflect a commitment to quality and reliability.
3. Customization Options
Every application may require specific dimensions and materials. A good supplier should offer customization services to meet your exact needs.
4. Technical Support and Customer Service
A responsive technical support team can greatly enhance your purchasing experience. They can assist with material selection, troubleshooting, and product usage questions.
5. Competitive Pricing
While cost is not the only factor, it is essential. Ensure the supplier offers fair pricing without compromising on quality.
The Future of Oil Seal Manufacturing
The future of oil seal manufacturing looks promising with advancements in technology and materials. The industry is witnessing innovations such as:
- Smart Materials: The development of materials that can adapt to changes in temperature and pressure could lead to more effective seals.
- 3D Printing: This technology could revolutionize production processes, allowing for rapid prototyping and customization.
Conclusion
In conclusion, oil seal manufacturing is a crucial aspect of maintaining the performance and reliability of diesel engines. Understanding the significance of oil seals, their manufacturing process, and the factors to consider when selecting a supplier can empower businesses to make informed decisions. By choosing the right oil seals, companies can enhance operational efficiency, reduce maintenance costs, and extend the lifespan of their machinery.
For those in need of high-quality oil seals and diesel engine parts, client-diesel.com is an exemplary choice, offering a range of products and expertise tailored to meet the demands of a diverse market. Investing in quality oil seals is investing in the durability and performance of your machinery.