Understanding Plastic Injection Mold Shops
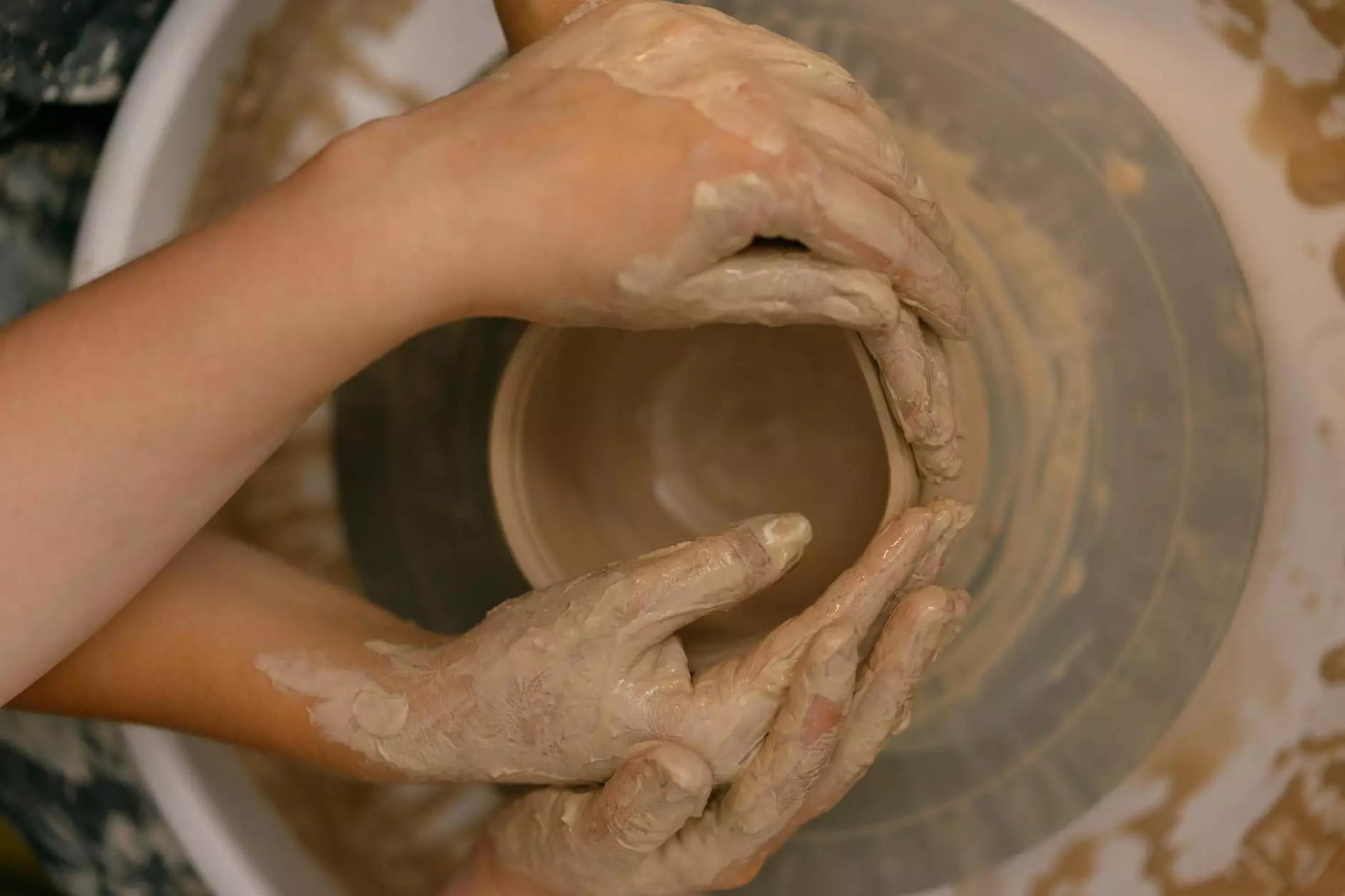
The world of plastic injection mold shops is a fascinating landscape filled with advanced technology, precision engineering, and exceptional craftsmanship. These facilities are crucial in various industries, producing high-quality plastic components that are integral to products we use daily. In this comprehensive guide, we will delve deep into the workings of plastic injection mold shops, their significance, and the processes that make them indispensable in modern manufacturing.
What is a Plastic Injection Mold Shop?
A plastic injection mold shop refers to a specialized facility that manufactures plastic parts through the process of injection molding. This technique involves injecting molten plastic into a mold cavity, which cools and solidifies to form the desired part. This process is renowned for its efficiency and ability to produce high volumes of uniform parts with minimal waste.
The Importance of Plastic Injection Molding in Manufacturing
Plastic injection molding has revolutionized the manufacturing industry for several reasons:
- Cost-Effectiveness: Once the initial setup and mold creation costs are covered, plastic injection molding offers one of the lowest production costs per unit.
- High Precision: The process provides high dimensional accuracy and consistency, ensuring that each part produced meets strict specifications.
- Versatility: Injection molding can handle a wide range of materials and can produce intricate designs that would be challenging to achieve with other manufacturing methods.
- Speed: The cycle time for injection molding is generally short, allowing manufacturers to produce large quantities of parts quickly.
The Process of Plastic Injection Molding
The process undertaken in plastic injection mold shops can be broken down into several critical steps:
1. Design and Engineering
The journey begins with a design phase where engineers create technical drawings and 3D models of the desired part. Advanced CAD (Computer-Aided Design) software plays a crucial role here, enabling precise designs that account for material properties and mold construction techniques.
2. Creation of the Mold
Once the design is finalized, the next step is to create the mold itself. This involves:
- Material Selection: Molds are typically made from steel or aluminum to ensure durability and longevity.
- Milling and Machining: Using CNC (Computer Numerical Control) technology, the mold is meticulously machined to match the design specifications.
- Finishing Touches: Additional processes, such as polishing and coating, are performed to ensure a smooth surface finish.
3. Injection Molding Process
The actual injection molding process consists of several key steps:
- Material Preparation: Plastic granules are fed into a hopper and heated until they melt.
- Injection: The molten plastic is injected into the mold under high pressure.
- Cooling: The mold is then cooled, allowing the plastic to solidify into the final part.
- Ejection: The mold opens, and the newly molded part is ejected for inspection and packaging.
Types of Plastic Injection Molding
Within the realm of plastic injection molding, several methods exist, each with its unique advantages:
- Standard Injection Molding: The most commonly used method, suitable for a vast array of products.
- Thin Wall Injection Molding: Ideal for products requiring lightweight and thin-walled designs, commonly found in food packaging.
- Gas-Assisted Injection Molding: Utilizes gas to create hollow parts and reduce the weight of the final product.
- Multi-Shot Injection Molding: Allows for the injection of two or more materials into a single mold, creating complex multi-material components.
Applications of Plastic Injection Molding
Almost every industry relies on plastic injection mold shops for manufacturing components. Here are a few notable applications:
- Automotive Industry: Production of parts like dashboards, panels, and lighting components.
- Consumer Electronics: Manufacturing casings for devices such as smartphones and laptops.
- Medical Devices: Creating components like syringes, housings for instruments, and disposable items.
- Household Products: These include toys, containers, kitchenware, and more.
The Role of Quality Control in Plastic Injection Mold Shops
Quality control is paramount in plastic injection mold shops to ensure that the produced parts meet both industry standards and customer expectations. This includes:
- Material Testing: Ensuring that the raw materials used are free from defects and meet the necessary specifications.
- Dimensional Inspection: Using tools such as calipers and gauges to measure the accuracy of the produced parts.
- Performance Testing: Conducting tests to assess the functionality and reliability of the final products.
The Future of Plastic Injection Molding
The landscape of plastic injection molding is ever-evolving, with new technologies and practices emerging to enhance efficiency and sustainability:
- Advancements in Materials: A push towards bioplastics and recycled materials is impacting the sustainability of the industry.
- Smart Manufacturing: The integration of IoT (Internet of Things) devices is allowing for real-time monitoring and optimization of production processes.
- Automation: Increased automation in the molding process can improve throughput and reduce labor costs.
Choosing the Right Plastic Injection Mold Shop
When selecting a plastic injection mold shop, several factors should be considered to ensure the best partnership:
- Experience: Look for shops with a proven track record in your specific industry.
- Technology: Ensure they are equipped with the latest machines and technology for efficient production.
- Customization: The ability to customize molds and parts to meet your specific needs is essential.
- Quality Assurance: Inquire about their quality control processes to confirm they adhere to industry standards.
- Customer Service: A responsive and supportive team can make the production process smoother and more productive.
Conclusion
In conclusion, plastic injection mold shops play a vital role in the manufacturing ecosystem, delivering high-quality plastic components essential for various industries. Their sophisticated processes, focus on precision, and adaptability to modern technology ensure they remain at the forefront of manufacturing. Choosing the right plastic injection mold shop can significantly influence your product development and production efficiency.
At Deep Mould, we pride ourselves on our ability to deliver superior plastic injection molding services tailored to meet the unique needs of our clients. With advanced technology, experienced engineers, and a commitment to quality, we are your trusted partner in manufacturing.